- 商务热线:
400-0371-828
- 企业传真:
0371-67890037
- 客服热线:
19149444863
18737157107
能源管理系统在化工领域应用与实践
发布时间:2019-06-28 浏览次数:
前言
化工工业是以能源为原材料的企业,其整个领域能耗占全国总能耗17%,而输出产品的70%以上为国民生活的必须品。因此,化工工业不仅是高能耗的领域,而且也是国民支柱性产业。
所以,降低化工行业单品的能耗水平,对于降低国民总能耗的水准有着重要的作用。而通过技术手段及工具,比如能源管理系统帮助化工工业建立科学、合理的能源管理指标,深化能源精细化运作。
通过能源管理系统对化工领域整个用能环节的分析与持续性改进,不断挖掘企业用能的改进空间,由被动节能转变为主动改造,最终实现运营成本下降。
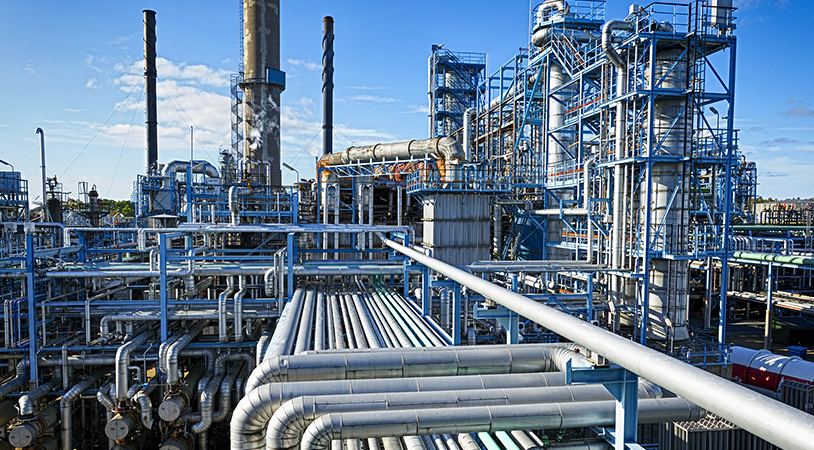
化工企业能耗管理面临的典型现状
如一家拥有年产20万吨碳酸氢铵的化肥厂,其完整的生产线包含造气、脱硫、净化、压缩、变换、精炼、碳化、合成多个工段,涉及的用能设备包含抽风机、炉前风机、破碎机、煤棒机、循环泵、干燥风机、压缩风机等多种设备。整个厂区的生产布局陈旧,各个生产线、生产设备之间的能耗情况不能进行能耗排名,造成管理与信息“孤岛”,进而诱发一系列的生产运营问题。
-
能源管理的基础工作薄弱
能耗监测设备落后,安装率和计量准确度不高,监测数据不能实现远传;需要运维人员进行人工抄录,易造成跑冒滴漏的现象且运维工作量大。
-
能耗管理机制不健全
能耗管理机制不健全主要围绕两个方面:降耗管理责任无法落实、节能降耗机制不健全。
(1)由于没有成体系的能耗数据,无法对关键设备、区域、部门、介质的能耗进行排名,因此造成数据的孤立,建立不起来能耗排名与考核机制。能耗管理自然就无法落到具体的责任人与责任部门,节能意识不能有效提升。
(2)无可视化的设备能耗信息,不能有效发现节能空间、节能改造计划无前后的验证数据对比,造成落后的能耗设备持续运营,有效的节能改造计划不能快速推广。
-
关键设备故障响应落后
设备故障通过巡检的形式发现,效率低下;不能预判关键设备的故障发生概率,当发生故障时,不能及时排查故障原因,造成由于设备故障造成的经济和运营损失持续扩大。
T@Energy 能源管理系统解决化工领域能耗管理问题
-
能耗数据管理与分析
通过能源管理系统对化工领域各个生产运营环节的能耗数据进行统计、分析、展现,实现对能耗数据全面的监测,为数据对比、节能改造方案效果验证、整体能耗分析奠定了基础。
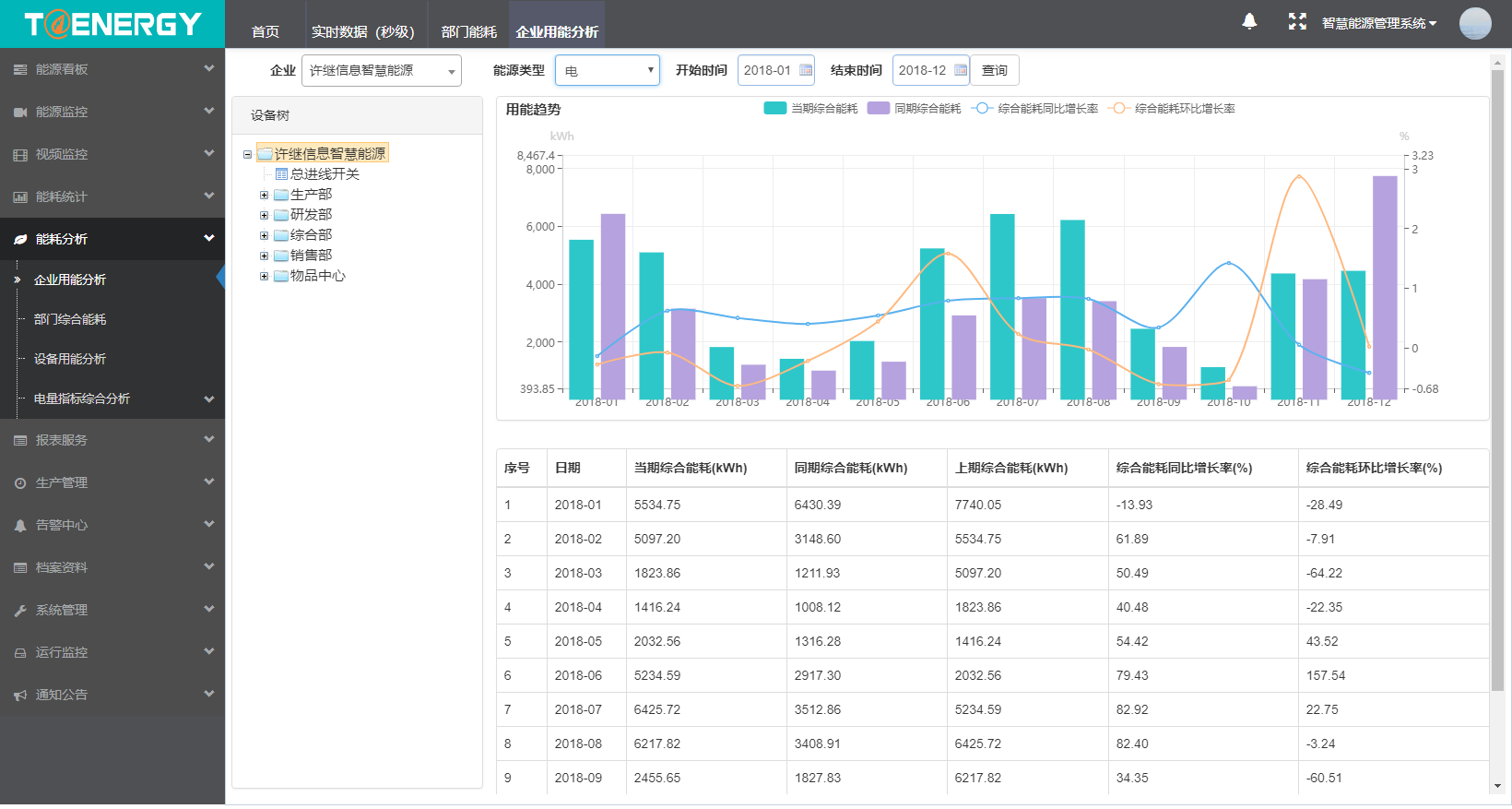
-
能源绩效管理
能源管理系统对关键的能耗设备和部门的能耗进行综合排名,帮助发现异常能耗情况以及部门之间能耗管理水平,为能源绩效考核给出了准确的数据。
-
关键设备管理
关键设备的故障发生是渐变到质变的过程,能源管理系统对关键设备的运行参数设置告警阈值,当触及告警阈值时,通过短信、弹窗、APP的形式对告警信息进行告知,化被动运维为主动运维,帮助运维人员预防关键设备的故障或准确判断故障信息,从而延长设备使用寿命、减少设备故障带来的经济损失。
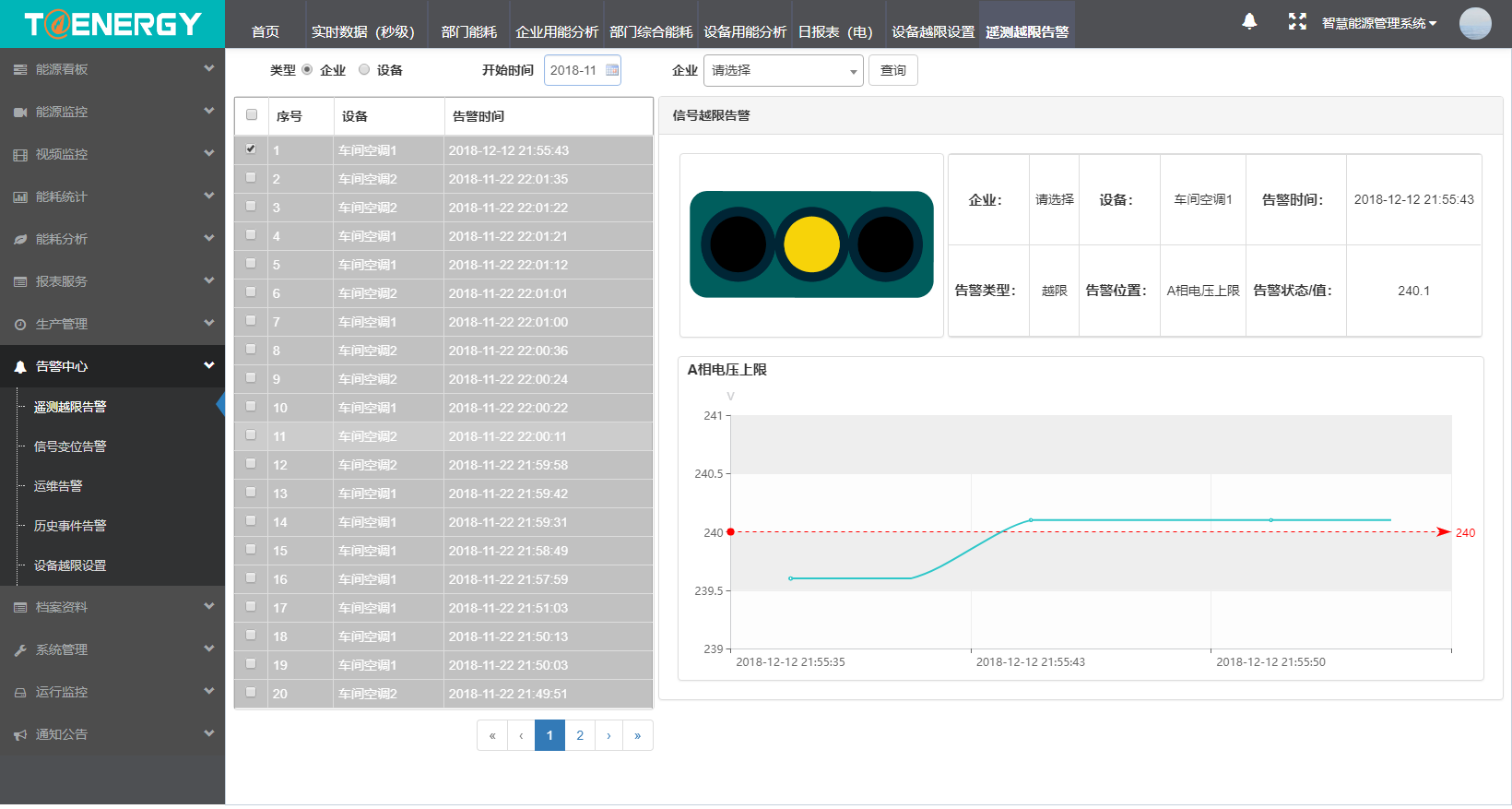
综上所述:
通过T@Energy智慧能源管理系统,化工行业将能耗数据进行多位一体的统一整合,打破管理孤岛和数据孤岛的现象,为精细化的能源管理、建立合理的用能考核标准、挖掘潜在的节能空间,实现化工企业可持续发展。
相关内容:关于政府推动能源管理系统平台建设的相关政策